KetaSpire PEEK XT-920 hebt die obere Temperaturgrenze von herkömmlichem PEEK deutlich an und eröffnet damit neue Anwendungsmöglichkeiten für spritzgegossene und bearbeitete Komponenten für diese Ultrahochleistungspolymere.
Mit dem gleichen 2:1 Verhältnis von Ether (E) zu Keton (K) weist Hochtemperatur-PEEK XT die gleiche außergewöhnliche chemische Beständigkeit auf wie herkömmliches PEEK. Diese polymere Struktur bietet auch eine bessere Beständigkeit gegenüber einer größeren Anzahl von Chemikalien als Polyketone wie PEK, PEKK, PEKEKK und PAEK, die ein etwas anderes Verhältnis von Ether zu Keton aufweisen.
Obwohl die chemische Beständigkeit mit der von PEEK vergleichbar ist, erhöht die einzigartige Chemie, die zur Entwicklung von PEEK XT führte, die Glasübergangstemperatur auf 170°C (338°F), d.h. 20°C (36°F) höher als bei früheren PEEK-Typen wie KetaSpire KT820 NT und Victrex 450G.
Aus KetaSpire PEEK XT spritzgegossene oder bearbeitete Komponenten behalten ihre Festigkeit auch bei extremen Temperaturen. Auf der Grundlage von Eigenschaftsdaten von Solvay, dem Hersteller von KetaSpire PEEK Polymeren, weist der XT-Typ einen um 400 Prozent höheren Zugmodul und eine um etwa 50 Prozent höhere Zugfestigkeit bei 160°C (320°F) als herkömmliches PEEK auf. Es bietet außerdem eine verbesserte Durchschlagsfestigkeit und einen höheren Volumenwiderstand, was es zu einem soliden Kandidaten für elektrische Hochtemperaturanwendungen macht.
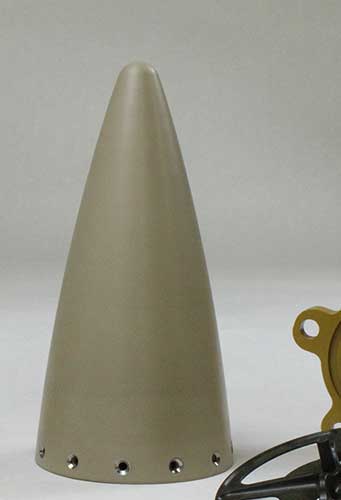
PEEK XT-Typen für spritzgegossene Komponenten
Solvay bietet KetaSpire PEEK in drei Qualitäten an: unverstärktes PEEK XT-920, sowie 30% Kohlefasern verstärktes KetaSpire XT-920 CF30 und 30% Glasfasern verstärktes KetaSpire XT-920 GF30. Die faserverstärkten Formulierungen bieten mehr strukturelle Festigkeit für Anwendungen, die hohen Belastungen und Drücken standhalten müssen.
Spritzgegossene Technologie für verstärkte und ungefüllte PEEK XT Polymere
Die Kunden erkennen die Kompetenz von Drake Plastics bei der Entwicklung von Werkzeugen, Prozessbedingungen und Anlagenkonfigurationen für hochentwickelte Polymere an, die spritzgegossene Teile mit präzisen Toleranzen, minimalen Spannungen und optimaler Leistung ergeben. XT920 wird bei viel höheren Temperaturen verarbeitet als PEEK, und sein Verarbeitungsfenster ist enger. Präzise Prozessgestaltung und -steuerung sind Schlüsselfaktoren, um die höheren Eigenschaften der KetaSpire XT PEEK-Typen zu erreichen, und dies gilt umso mehr für die mit 30% Glasfasern oder Kohlefasern verstärkten Formulierungen.
Schmelzflussanalyse als Wegweiser:
Das Labor von Drake Plastics verfügt über die analytischen Werkzeuge, um die Fließeigenschaften der Polymere zu bestimmen, die als Leitfaden für die besten Verarbeitungsparameter und das Werkzeugdesign für jeden PEEK XT-Typ dienen.
Unsere Werkzeugexperten nutzen die Informationen für das Design der Anschnitte, um eine Faserorientierung zu erreichen, die die Festigkeit der spritzgegossenen Komponenten optimiert. Die Analysedaten definieren auch die Prozessbedingungen, die die inhärenten Eigenschaften der einzelnen PEEK XT Typen erhalten.
Die Technologie des spritzgiessen optimiert Leistung und Qualität:
Drake Plastics setzt vollelektrische Maschinen zum Spritzgiessen ein, die konstant und effizient arbeiten und das Risiko von Hydrauliklecks oder -verschüttungen ausschließen.
Unsere Ingenieure passen die Abmessungen der Fässer an das jeweilige Polymer an, um die Zeit bei der Temperatur während des Spritzgießens zu minimieren. Dies verhindert den Abbau des Polymers in der Schmelzphase und gewährleistet maximale Eigenschaften und Konsistenz jedes spritzgiessen Stücks.
Die Investition von Drake Plastics in RJG-Kontrollsysteme trägt weiter zur gleichbleibenden Qualität und Leistung der spritzgegossenen PEEK XT-920-Komponenten bei. Das Gerät überwacht die Bedingungen im Werkzeughohlraum und hält die idealen Prozesstemperaturen und -drücke für jede PEEK XT-920 Qualität aufrecht.
Zu den Hochtemperaturanwendungen von PEEK XT gehören große Bauteile mit starken Wandstärken, bei denen es beim Spritzgiessen zu Oberflächensenkungen oder inneren Hohlräumen kommen kann. Die spritzgegossenen Maschinen von Drake Plastics sind mit einer Kompressionsfunktion ausgestattet, die es ermöglicht, dickwandige Teile während des Abkühlungszyklus zu konsolidieren. Durch diese Nacheinspritzung wird das Teil in der Form komprimiert oder „geprägt“, so dass dickwandige Teile ohne Hohlräume oder Porosität entstehen.
Vielseitig in der Abmessung:
Maschinenabmessungen zwischen 35 und 300 Tonnen bieten den Kunden eine Auswahl an spritzgegossenen Komponenten von 0,85 Gramm (0,03 oz.) bis 567 Gramm (20 oz.). Diese Fähigkeit dient der vielfältigen Palette von Anwendungen in der Öl- und Gasindustrie, von elektrischen Präzisionskomponenten bis hin zu großen Ventilen und Dichtungen.
KetaSpire Hochtemperatur PEEK XT Anwendungen
Die drei Qualitäten von KetaSpire XT-920 eignen sich ideal für Komponenten, die Temperaturen ausgesetzt sind, die über dem Tg-Wert herkömmlicher PEEK-Qualitäten liegen, wo sie schnell an Festigkeit und Steifigkeit verlieren und ihre Wärmeausdehnungsrate dramatisch ansteigt. Auch die elektrischen Isolationseigenschaften nehmen bei Temperaturen über der Tg eines Polymers drastisch ab.
NORSOK M710 Sauergas-Tests haben die Fähigkeiten des Polymers für Anwendungen in Bohrlochumgebungen gezeigt. Nach einer 50-tägigen Einwirkung von 20%H2Sbei 230°C und einer 14-tägigen Einwirkung von Sole/HC bei 300°C zeigte PEEK XT eine vergleichbare Leistung wie herkömmliches PEEK, ein Material, das weltweit für seine Zuverlässigkeit bei Komponenten für Öl- und Gasanlagen bekannt ist.
Zu den typischen Anwendungen, bei denen PEEK XT als Upgrade für höhere Temperaturen im Vergleich zu herkömmlichem PEEK eingesetzt werden kann, gehören Ventilsitze, Dichtungen und Back-up-Dichtringe, elektrische Anschlüsse in ESPs, Spulen und Radome.
Prototypen und Komponenten, die aus KetaSpire PEEK XT Halbzeugen hergestellt werden
Drake Plastics extrudiert alle Qualitäten von KetaSpire PEEK XT-920 zu maschinell bearbeitbaren Stäben und Platten in Lager- und kundenspezifischen Abmessungen. Unsere CNC-Bearbeitung wandelt diese Halbzeuge routinemäßig in Prototypen um, um das Design und die Leistung der Komponenten zu testen und zu validieren, bevor wir in Spritzgießwerkzeuge investieren. Wir unterstützen unsere Kunden auch bei der Herstellung spanend bearbeiteter Teile, falls diese benötigt werden, bevor die Werkzeuge für die Produktion fertiggestellt sind.
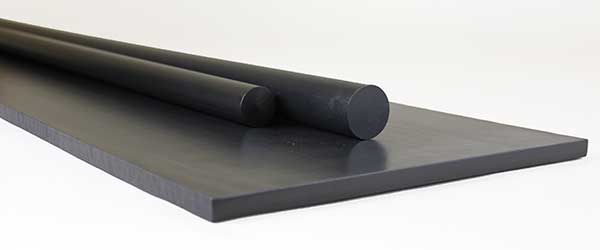